高明利 任海涛 马文波河南省矿山起重机有限公司 长垣 453400
摘 要:电动单梁起重机主梁制造用的U 形槽是该类型起重机主梁的重要组成部分,传统的生产方法为分段压制成形,并进行焊接组合加长,但该方法存在许多缺陷,影响起重机质量、限制起重机大批量生产等。为解决传统方法存在的问题,设计并使用一种连续滚碾成形工艺技术,生产制造电动单梁U 形槽,取消了U 形槽组合加长焊接工序;通过量化分析,U 形槽连续滚碾成形工艺具有许多优越性。
关键词:U 形槽制造;连续滚碾工艺;结果分析
中图分类号:TG335.4 文献标识码:A 文章编号:1001-0785(2020)12-0060-04
0 引言LD电动单梁主梁是该类起重机最主要的承载部件,同时也是电动葫芦小车的运行轨道,因此电动单梁主梁的质量直接影响着起重机的安全使用,在这其中,制造工艺方法又是决定产品质量的关键因素。
传统的主梁制作工艺是:主梁U 形槽翻转口向上置于工装胎具上,调直、调平、垫出上拱度;按图纸要求栽焊隔板、焊接工字钢、焊接侧板、焊接斜板、焊接挂板等完成主梁制作。长期以来电动单梁起重机主梁U形槽的生产制造工艺方法是用液压设备分段压制短节U形槽,工艺设备如图1 所示,这种生产制造方法由于受钢板幅面宽度以及液压工作台宽度限制,U 形槽每节长度一般为1 500 mm,需将多段U 形槽短节组合焊接成满足起重机跨度要求的长条U 形槽,见图2。按照这种传统工艺方法生产制作出的单梁主梁存在许多问题,例如:由于焊接应力集中主梁负载后容易下挠变形、主梁U 形槽焊缝处易出现疲劳破坏、主梁旁弯大影响葫芦小车运行等,同时存在浪费原材料、生产效率低的问题。为了解决上述问题,特研制了新式电动单梁起重机主梁U 形槽连续滚碾工艺技术(以下简称连续滚碾工艺),采用连续滚碾工艺,取得创新性成功,工艺设备如图3所示。传统工艺与连续滚碾工艺生产制造的U 形槽如图2、图4 所示,与传统工艺相比,采用连续滚碾最终生产的主梁实物无横向焊缝,见图5、图6。

图 1 传统短节压槽工艺设备

图 2 传统工艺成型的短节U 形槽

图 3 无接缝U 形槽滚碾工艺设备

图 4 连续滚碾工艺成型的无接缝U 形槽

图 5 传统工艺生产的主梁实物

图 6 连续滚碾工艺生产的主梁实物
1 U 形槽连续滚碾工艺原理电动单梁起重机主梁U 形槽连续滚碾工艺技术,改变传统的上下垂直挤压成形方式( 见图7a)。U 形槽水平延伸连续渐变滚压成形输出。成形工艺原理简图如图7b 所示,主要包括工序过程为:1)首先按照产品U 形槽周长并考虑滚碾延伸率定制符合U 形槽周长尺寸要求宽度的板卷;2)将钢板卷安装在滚碾开卷机上,启动设备,由喂料机构拉伸卷板头给开平工部送料,卷板拉伸后在平板区擀平,再传递给渐变成形碾制区滚碾成形。滚碾成形后的U 形槽继续向前输送进入整形区,通过整形区整形进一步提高U 形槽工件精度,从而达到设计要求;3)定长剪切U 形槽 由于辊碾机为连续滚碾工作,理论上钢板长度足够长,工作场地足够长,U 形槽长度可以不受限制的延长,生产中只需要根据起重机的跨度要求剪切断开U 形槽。现实生产中需根据合同要求将跨度参数编程,通过设置所需U 形槽长度,滚压到一定长度可自动剪切,直接制造出合格的U 形槽工件。
目前根据市场需要以及运输长度限制,31 m 及以下跨度的电动单梁起重机主梁U 形槽均可以实现连续成形,不需要对接。
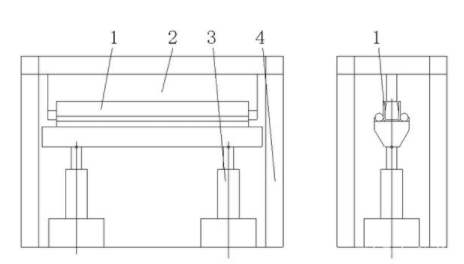
1.U 形槽 2.U 形槽压型 3. 液压机 4. 液压机机架(a)U 形槽传统压形工艺原理图

1. 钢卷 2. 钢板擀平区 3. 成形区 4. 整形区 5.U 形槽(b)U形槽辊轧成形连续滚碾工艺原理图图 7 成形工艺原理简图
2 工艺对比分析2.1 耗材对比以LD5t-22.5m 跨度电动单梁主梁U 形槽为例,将两种工艺方法制造出来的产品进行对比分析。U 形槽材为Q235B,截面尺寸为-6×452×575 mm,跨度22.5m 主梁所需U 形槽长度为222 20 mm。1)钢板原材料浪费情况对比分析采用连续滚碾工艺可以直接制造出截面,避免钢材原材料浪费的问题;传统工艺生产制作U 形槽,必须分段制作,每段长度1 500 mm,组合成222 20 mm 长度需要为14.813 节,故制造生产一台5 t 跨度22.5m 的主梁U 形槽,需要用15 节1 500 mm 的短节组合焊接一起才能实现,其中,多余的U 形槽长度280 mm 这一段原材料属于浪费料。因而可得浪费料折合质量为1570.26×0.006×0.28×7.85=20.71 kg,可见相比使用传统方法,连续滚碾成形工艺可节约20.71 kg 钢板原材料。
2)U 形槽组合焊接焊条原材料消耗对比分析采用传统的分段组合焊接有14 道U 形焊缝需要焊接,焊缝高5 mm, 焊缝宽10 mm,14 道焊缝需要的焊接焊条质量为15×2×1570.26×0.005×0.01×7.85=18.94 kg,采用连续滚碾工艺生产制造U 形槽无对接接口,不需要消耗焊接焊条。
2.2 制造工时对比分析若采用传统的分段压槽组合焊接成形工艺,需要15 段短节U 形槽组合焊接成形,经现场计时考察需要以下工序时间完成:1)上料- 压槽- 出槽每节需时5 min,15 节合计需时75 min;2)短节U 形槽放置工装胎具上每节需时5 min,15 节合计需时75 min;3)找正、点焊每一个接口需单个接口需时5 min,14 个接口合计需时70 min;4)U 形槽焊接每米需时1 min,14 个接口焊接合计需时44 min;5)平均每个接口需焊条8 根,更换单根需时 0.5min,14 个接口合计需时56 min;6)调整焊接位置、工件翻转平均每个接口需时5min,14 个接口合计需时70 min;7)清理焊渣、药皮每个接口需时1 min,14 个接口合计需时14 min。
不考虑焊U 形槽焊接后整形时间,采用传统的分节压制成型,然后进行组合,所需工序时间为404 min;采用连续滚碾成形工艺制造相同规格U 形槽,直接使用设备制造,需时为2.222 min;与传统工艺相比,采用连续滚碾工艺可节约时间401.778 min;
2.3 工件强度质量影响对比分析1)不同工艺对U 形槽构件疲劳强度的影响分析使用传统工艺分段压制成形,然后再焊接组合成形制造出来的U 形槽,接口处为U 形连续焊接焊缝,焊接件的焊接应力集中等级为K4 级,U 形槽构件工作级别为E4,拉伸和压缩疲劳许用应力的基本值为[1]:[σ-1]L=62.2 MPa
采用连续滚碾成形工艺制造U 形槽,U 形槽中间无焊缝,拉伸和压缩疲劳许用应力基本值为[1]:[σ-1]X=182.1 MPa比较两种情况的疲劳强度许用应力基本值,可知在其它条件相同的情况下,连续滚碾工艺制作的工件强度要明显的高于老工艺制作的工件强度。
2)脆性破坏因素分析如图5 所示,采用传统工艺分段压制成形U 形槽,再组合成长条成品U 形槽制成的电动单梁主梁存在着许多纵横交叉焊接焊缝,焊缝汇聚,属于高度应力集中现象,工件脆性破坏的危险性最大,脆性应力影响评价系数ZA=σG/0.3σS+1
表明结构件材料受焊接影响的脆性严重。采用连续滚碾成形的U 形槽制造而成的电动单梁主梁,该主梁没有U 形对接焊缝,主要有4 条纵向焊缝,如图6 所示, 构件焊缝评级应为I 类焊缝,此种情况脆性应力影响评价系数ZA=σG/0.3σS-1
表明结构件脆性破坏的可能性比较低。可知,采用连续滚碾工艺制造的主梁强度明显高于传统工艺制造的主梁,连续滚碾工艺制造的起重机安全系数明显高于传统工艺制造的起重机。
2.4 工人劳动强度影响对比分析就U 形槽制作而言,分段压型的传统工艺,很难实现机械化和自动化,板料上料和U 形槽卸料都是由人工搬抬完成。要制作跨度22.5 m 使用的22 220 mm 长的U 形槽,仅压型一道工序,工人需要将15 节U 形槽板料和U 形槽分别搬上和搬下15 次,而压槽工作台高度一般800 mm,每节U 形槽重量为110.94 kg,工人需要承担巨大的劳动强度。
采用连续滚碾成形工艺,生产过程中,上钢板卷和下22 220 mm 长的U 形槽采用的是起重机吊装方式,工人无需搬抬做功,大大降低了劳动强度。
2.5 工艺对比分析小结使用连续滚碾工艺制造的产品,表面没有对接焊缝,显著减少制作时的相关焊接工作量,焊接材料消耗明显降低。同时减少焊缝数量,减少了焊接应力集中,焊接变形明显减小,工件内在质量明显提高。起重机产品性能和几何尺寸明显提高,同时提高了安全系数。
3 结语采用连续滚碾制造电动单梁主梁U 形槽的新工艺技术,具有明显的经济效益;同时显著的降低工人劳动强度、改善生产环境、提高生产效率;采用连续滚碾工艺方法进行相关生产制造,可以显著提高主梁钢结构质量,提高起重机安全使用可靠度、保证电动葫芦小车运行通畅。
参考文献[1] GB/T3811—2008 起重机设计规范[S].[2] JB/T1306—2008 电动单梁起重机[S].[3] 张质文 起重机设计手册[M]. 北京:铁道出版社,2013.